This webinar will present strategies and tools for doing a complete and comprehensive impact assessment of supplier change notices. Tools and procedures for deciding if full impact assessments need to be processed and when notices for lower impact changes can be accepted or rejected without a full assessment will be discussed. Who (what skill sets) should be on the impact assessment team, how often to meet and methods for evaluating change notices will also be discussed. Supplier agreements and quality agreements with suppliers and vendors as well as using risk based approaches to impact assessments will be highlighted.
WHY SHOULD YOU ATTEND?
Any manufacturer of pharmaceutical products or medical devices will have vendors and suppliers in order to acquire the materials needed for manufacturing product. In a regulated environment, the manufacturer is responsible for the quality and source of all incoming materials. When supplier or vendors make changes to material, its own manufacturing or supplier they should tell the manufacturer about these changes via a supplier change notice. Without proper evaluation of the change, unforeseen changes could occur in the product leading to failed manufacturing runs or the release of non-conforming material to market. Regulatory agencies (FDA) expect manufactures to be in control of all incoming material, therefore failure to do a proper impact assessment of supplier changes could also lead to enforcement action and/or product recall. Manufactures need a robust process ensure all vendors and suppliers provide change notices and to evaluate all notices for impact.
AREA COVERED
- Introduction to supplier change notices
- Regulatory impact of supplier change notices
- Risk based approach to categorizing supplier change notices
- Key skill sets needed to evaluate supplier change notices
- Verification and Validation of supplier change notices
- Key tools to help in impact assessments of supplier change notices
LEARNING OBJECTIVES
- Understanding supplier change notices
- Categorization of change notices based on risk
- Setting up a change impact team
- Supplier/vendor quality agreements and supplier agreements
- What happens if the change is unacceptable
- How to set up incoming material specifications
WHO WILL BENEFIT?
- QA professionals
- Technical scientists
- Production staff
- Regulatory Affairs professionals
- Supply chain professionals
Any manufacturer of pharmaceutical products or medical devices will have vendors and suppliers in order to acquire the materials needed for manufacturing product. In a regulated environment, the manufacturer is responsible for the quality and source of all incoming materials. When supplier or vendors make changes to material, its own manufacturing or supplier they should tell the manufacturer about these changes via a supplier change notice. Without proper evaluation of the change, unforeseen changes could occur in the product leading to failed manufacturing runs or the release of non-conforming material to market. Regulatory agencies (FDA) expect manufactures to be in control of all incoming material, therefore failure to do a proper impact assessment of supplier changes could also lead to enforcement action and/or product recall. Manufactures need a robust process ensure all vendors and suppliers provide change notices and to evaluate all notices for impact.
- Introduction to supplier change notices
- Regulatory impact of supplier change notices
- Risk based approach to categorizing supplier change notices
- Key skill sets needed to evaluate supplier change notices
- Verification and Validation of supplier change notices
- Key tools to help in impact assessments of supplier change notices
- Understanding supplier change notices
- Categorization of change notices based on risk
- Setting up a change impact team
- Supplier/vendor quality agreements and supplier agreements
- What happens if the change is unacceptable
- How to set up incoming material specifications
- QA professionals
- Technical scientists
- Production staff
- Regulatory Affairs professionals
- Supply chain professionals
Speaker Profile
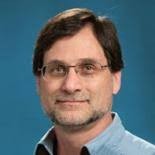
Alan M Golden has over 30 years of experience in the medical device industry, both in basic research and quality assurance. Alan spent 31 years at Abbott Laboratories. For the first 16 years as part of diagnostics R&D, he developed recombinant proteins used in diagnostics tests, received three US patents, and published numerous papers and abstracts. Alan then transitioned to a quality assurance role wherein both the Abbott Diagnostics and Abbott Molecular divisions, he was responsible for quality assurance for new product development, on-market product support, and operations.Alan’s quality assurance experience extends from design control, change control, risk …
Upcoming Webinars
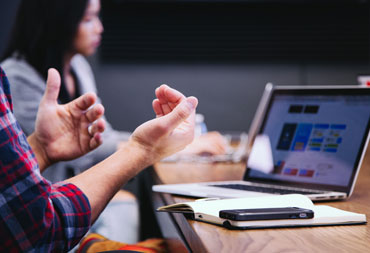
3-Hour Virtual Boot Camp on Easier Excel Automation with VB…
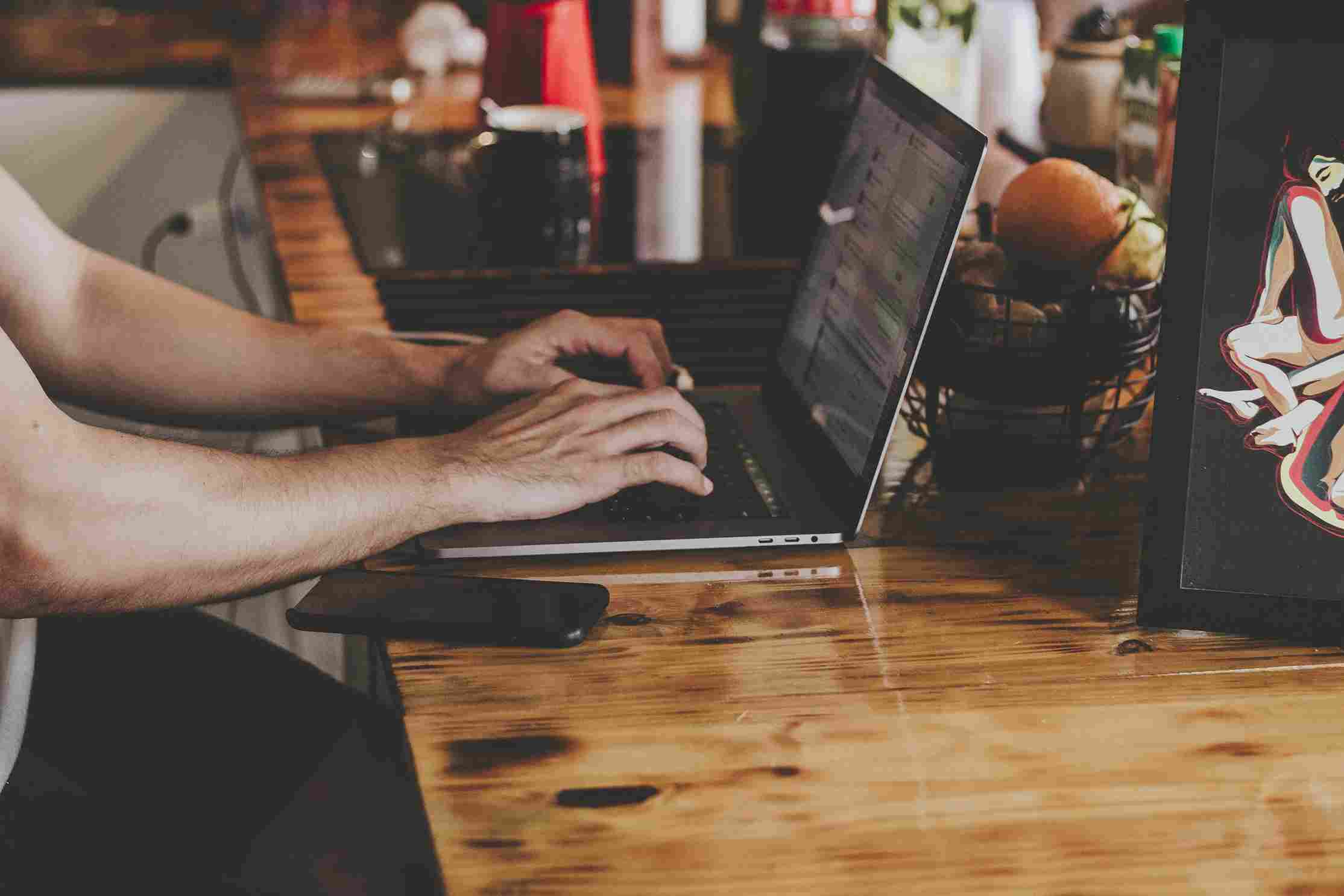
Outlook - Master your Mailbox - Inbox Hero Inbox Zero
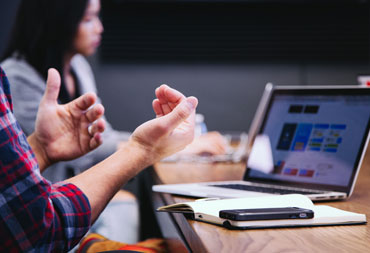
Retention Starts Here: Stop Losing Your Critical Talent and…
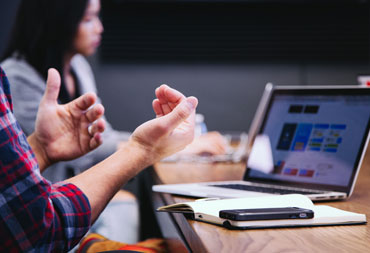
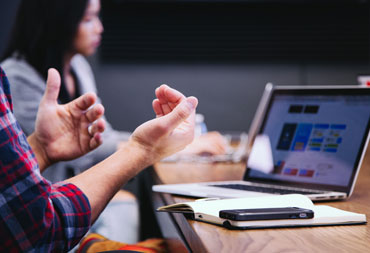
Empowering Conflict Resolution: Letting Go to Gain Control
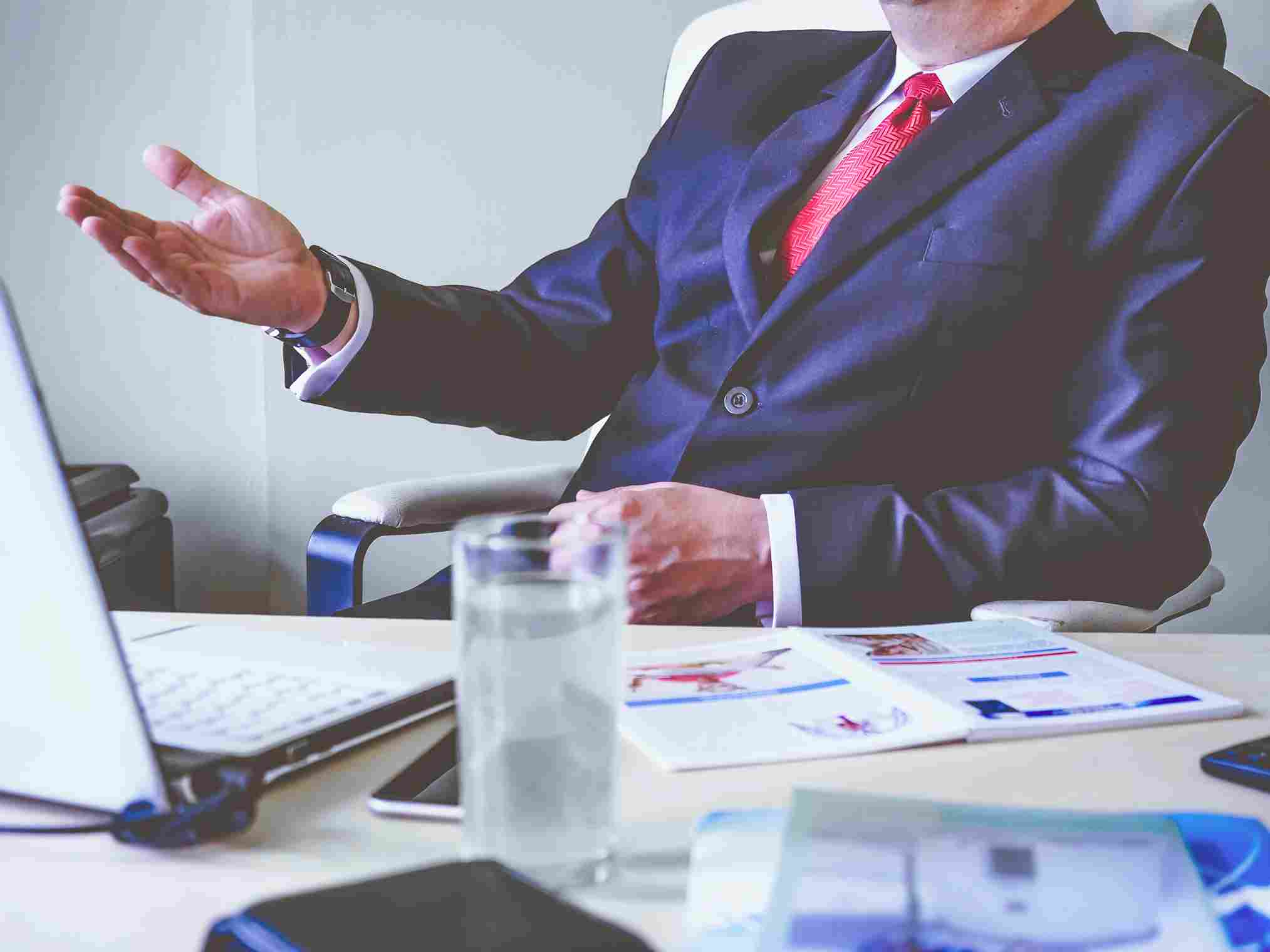
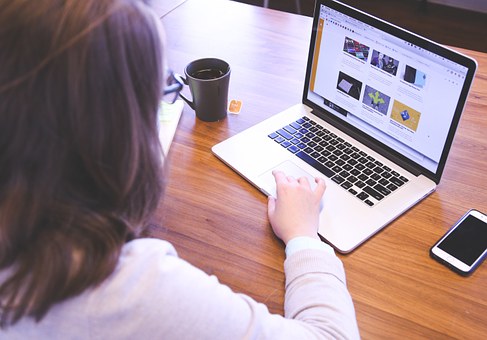

California Meal and Rest Breaks: What You Don't Know Can Co…
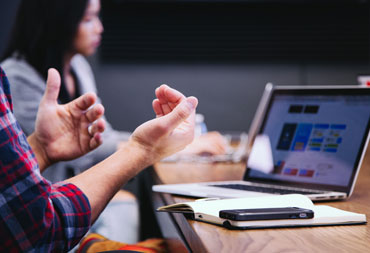
Gossip-Free: Leadership Techniques to Quell Office Chatter
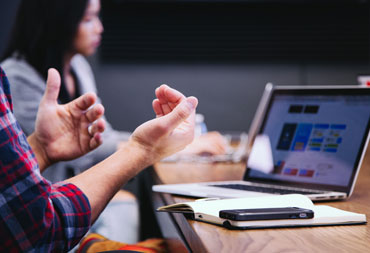
Managing Difficult Employee Conversations
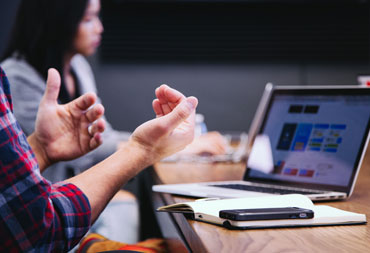
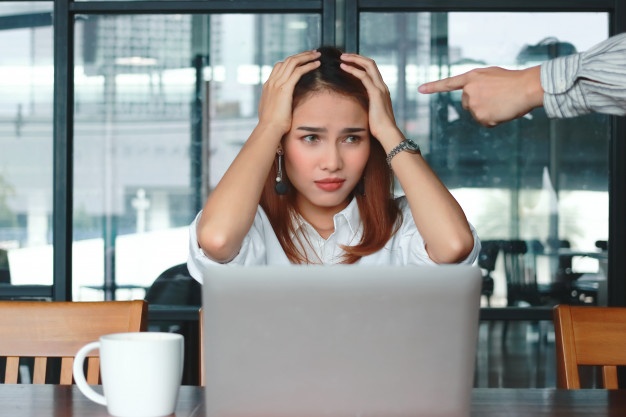
Harassment, Bullying, Gossip, Confrontational and Disruptiv…
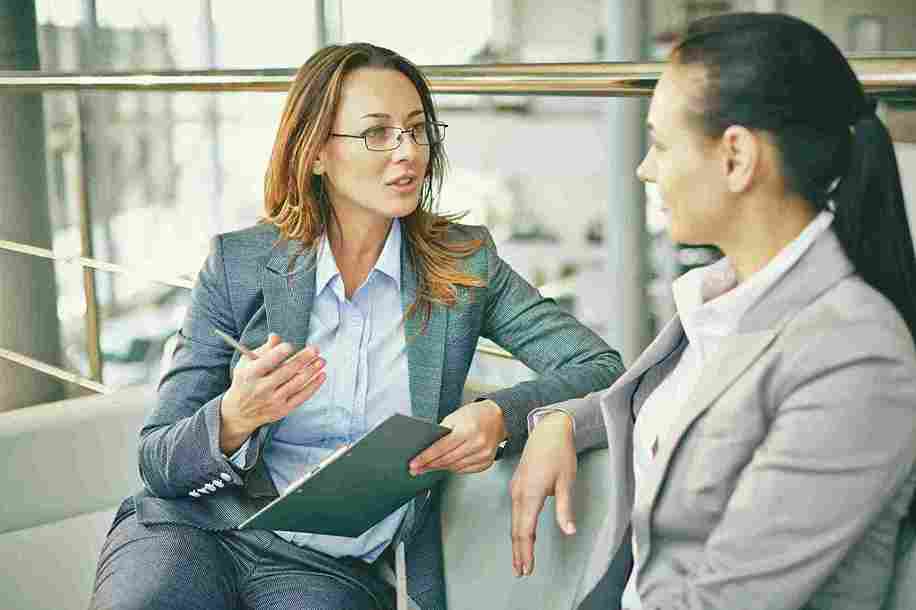
Managing Toxic Employees: Strategies For Leaders To Effecti…
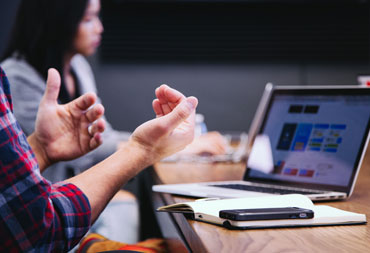
Workplace Investigations 101: How to Conduct your Investiga…
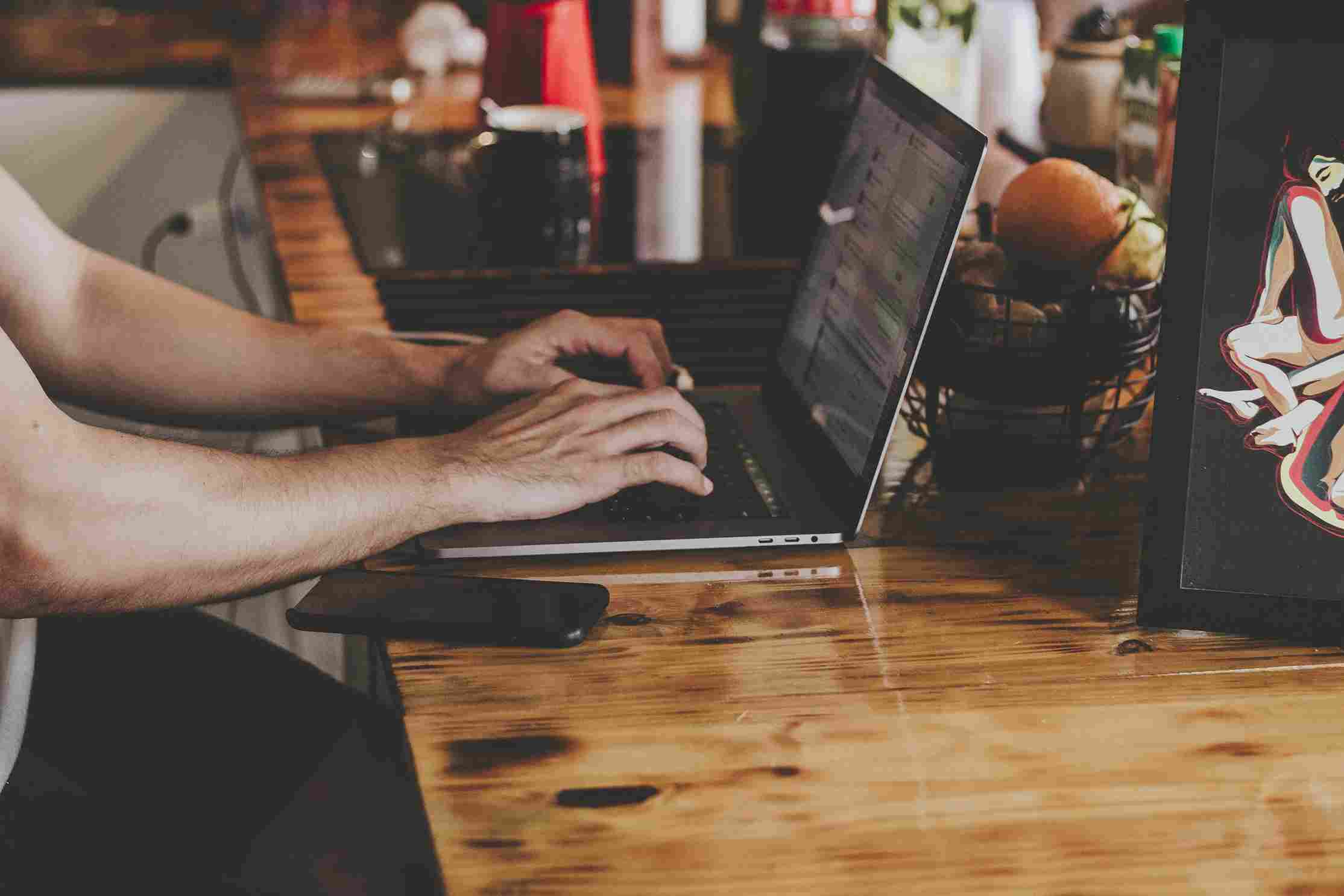
Excel Power Skills: Master Functions, Formulas, and Macros …
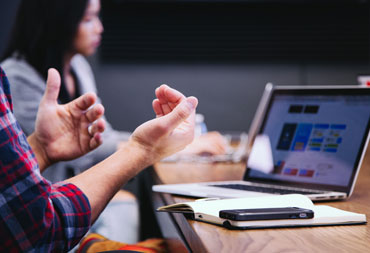
Copilot and HR: An Introduction for HR Professionals
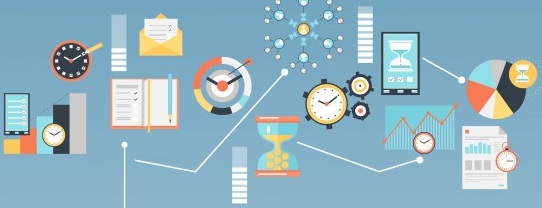
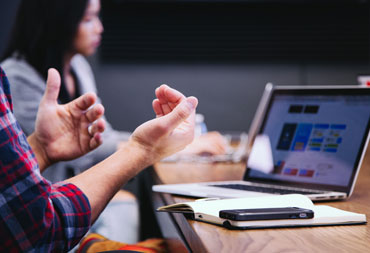
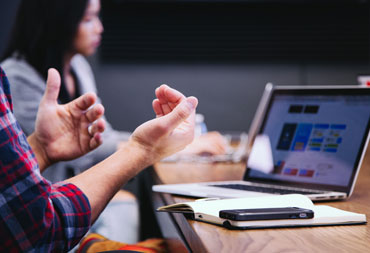
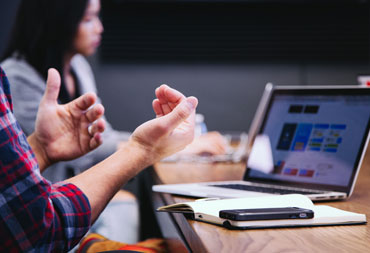
Bootcamp for New Managers and Supervisors: Develop These Es…
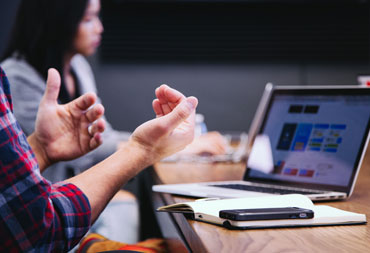
6-Hour Virtual Seminar on Learning the Highlights of Excel …
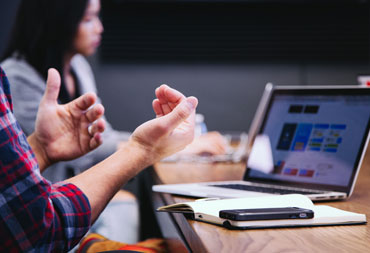
Stress, Change And Team Resilience Through Humor: An Intera…
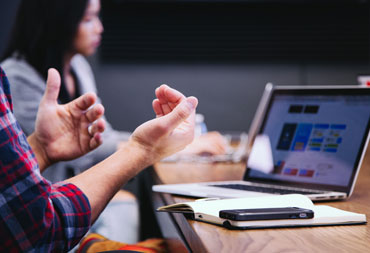
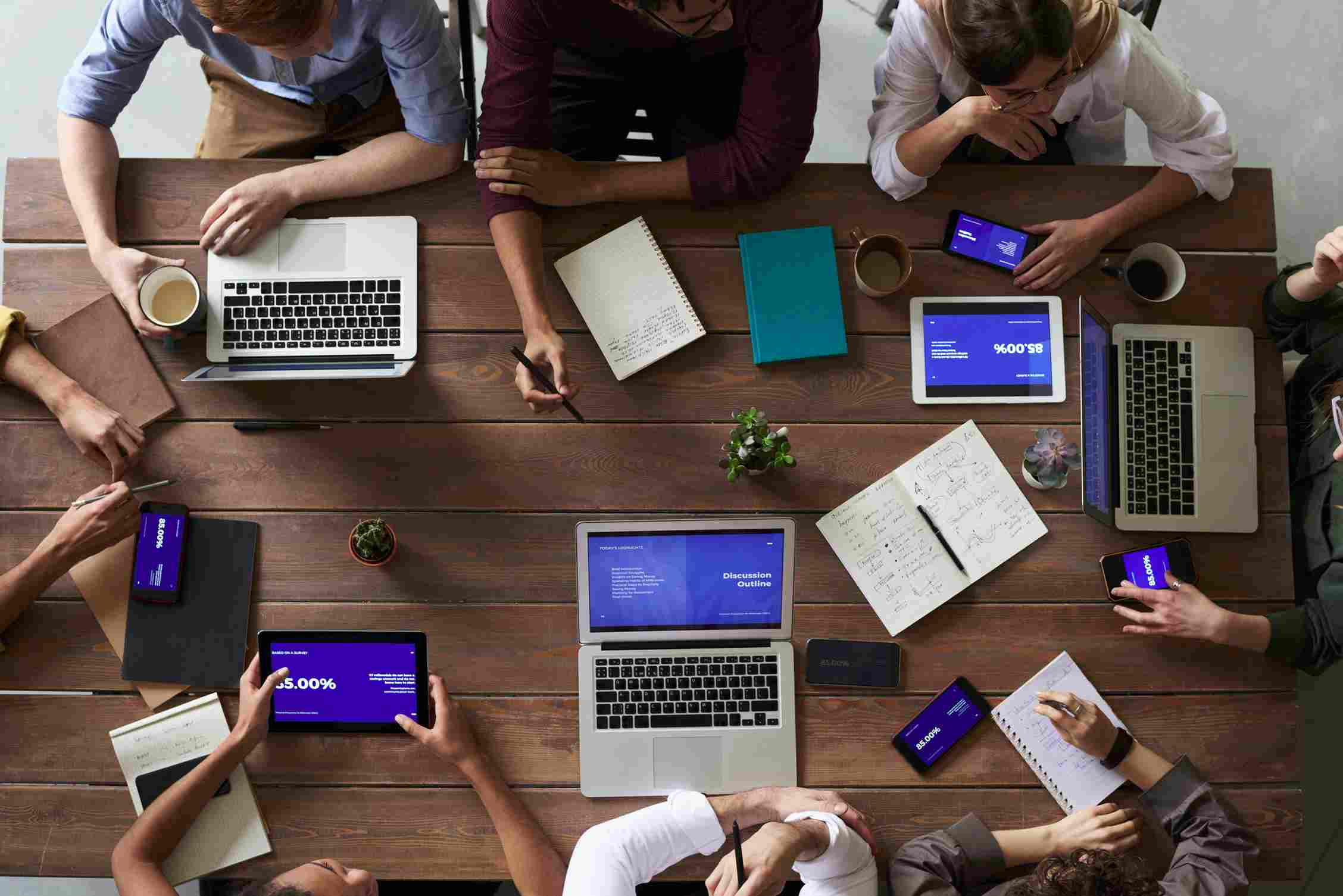
Project Management for administrative professionals
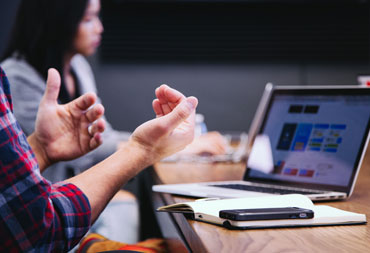
Is Your Workforce Change Ready? A Leader’s Guide to Quickly…
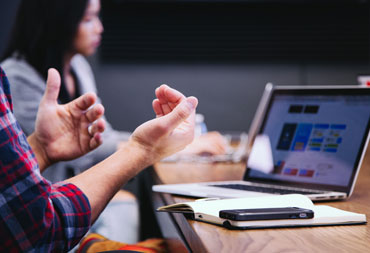
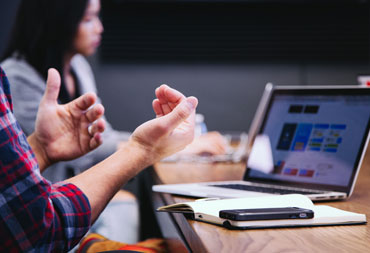
The Importance of the first 5 seconds when presenting
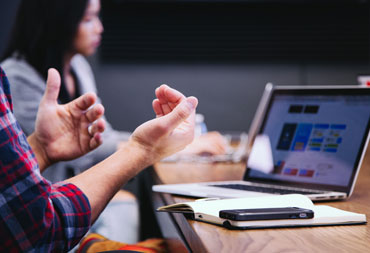
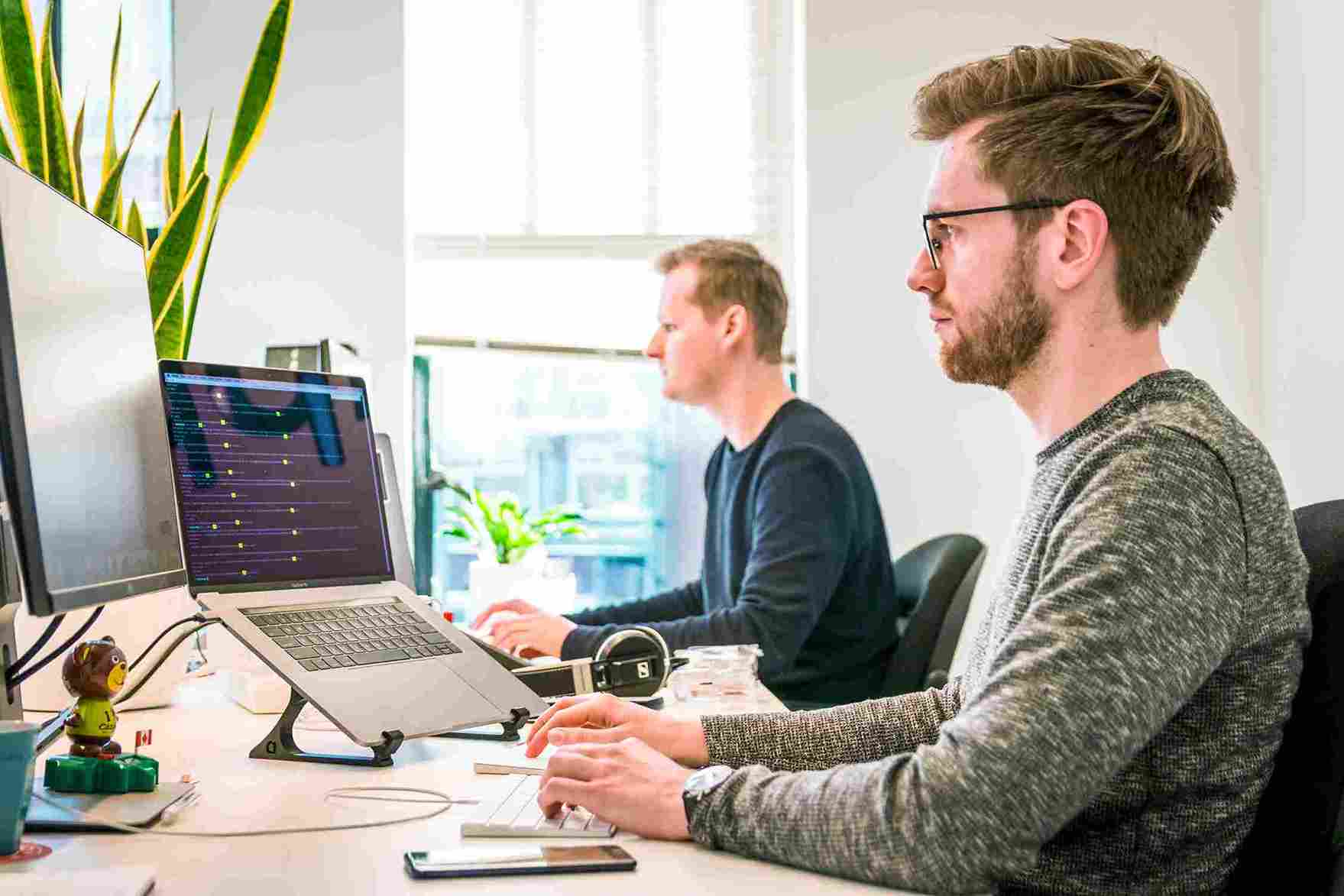
Emotional Intelligence: Mastering the Emotions of Great Lea…